BOSS
Home / Forged Fittings / BOSS
FORGED FITTINGS
Products
Get a Free Quote
Toll Free Call :
+91 93216 51417
COPPER NICKEL BOSS
The Copper-Nickel Boss from Nexus Alloys and Steels are made from a copper-nickel alloy, which combines the beneficial properties of both copper and nickel. This alloy is known for its excellent resistance to corrosion and erosion, especially in marine environments. The forging process involves heating the copper-nickel alloy until it’s malleable, then applying high pressure to shape it into the desired form. This process enhances the strength and durability of the Bosses. These Bosses from Nexus Alloys and Steels provide a contoured internal joint with a gradual transition from header to branch allowing full penetration welds while reducing installation costs over tees or other nozzle connections. They are used to connect different sections of a pipe or to adapt different sizes of pipes to each other, providing a tight, leak-proof seal
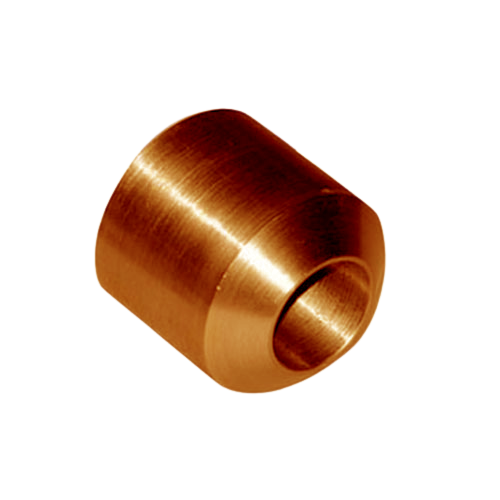
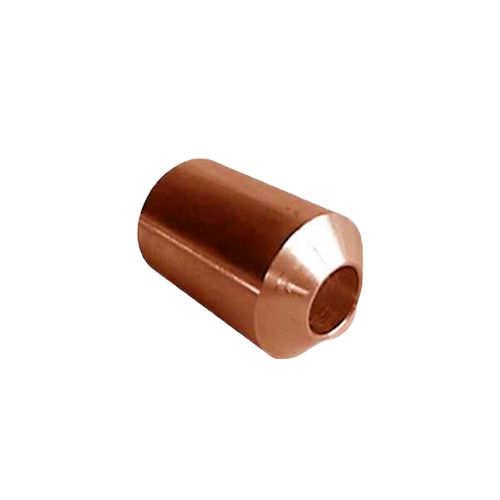
DESCRIPTION
Copper-nickel forged fitting Bosses typically have a outer shape for easy wrench grip. The interior is hollow and threaded to allow for secure attachment to pipes. Due to their robustness and resistance to corrosive elements, these Bosses are commonly used in industries such as shipbuilding, desalination plants, offshore oil and gas platforms, and power generation
Key Features of Copper-Nickel Boss
- Reliability : They are crafted in accordance with international and national standards, adhering to rigorous quality norms. This makes them a reliable choice for even the most demanding applications
- Enhanced Sealing : These fittings outperform in mechanical sealing, proactively averting leaks and mitigating the potential for system failures
- Tightening Properties : Bolstered by supplementary tightening attributes, these fittings guarantee a secure and unwavering connection between diverse components
- Chemical and Hydraulic Compatibility : They are engineered with superior chemical and hydraulic attributes, demonstrating remarkable resilience across a broad spectrum of fluids and diverse conditions
- Durability : These fittings are designed for enduring performance, even within challenging environments. They are vital in sectors like aerospace, nuclear power, and automotive
- High-Pressure Capability : They flourish in high-pressure conditions ranging from nuclear power plants to oil and gas facilities, playing a pivotal role in enhancing operational safety and efficiency
GRADES
- Copper Nickel 90/10 (C70600) : Comprised primarily of 90% copper and 10% nickel, with additional small amounts of iron and manganese, this material is fortified to improve its corrosion resistance. Its exceptional ability to withstand seawater corrosion renders it highly favored for marine applications
- Copper Nickel 70/30 (C71500) : Consisting of 70% copper and 30% nickel, along with minimal amounts of iron and manganese, this material delivers enhanced corrosion resistance. It is employed in applications requiring heightened resilience
TECHNICAL SPECIFICATION
- Dimensions : B16.11 and BS 3799
- Size : The size of the fitting ranges from 1/4" NB to 4" NB
- Pressure Class : The pressure class of the fitting can be 3000 LBS, 6000 LBS, or 9000 LBS
- Type : The fitting can be of the type Socket Weld (S/W) & SCREWED (SCRD) – NPT, BSP, BSPT
- Material : The fitting is made from Copper-Nickel alloys. The common grades used are Copper Nickel 90/10 (C70600) and Copper Nickel 70/30 (C71500)
- Applications : These fittings are used in shipboard and offshore drilling piping systems, industrial condensers, heat exchangers, evaporating equipment, and power installations
- Ends : Boss outlets can be supplied with threaded, socket welding, or butt welding ends
SERVICES & CERTIFICATES
- Testing Facility Available : Radiography test, Chemical Analysis, Mechanical Tests, Ultrasonic test, PMI test, Hydrostatic test, Corrosion test, Metallography Test, Miscellaneous test
- Test Certificates : Manufacturer Test Certificates as per EN 10204 type 3.1 and 3.2 as well as NABL lab test reports