END CAP
Home / Forged Fitttings / END CAP
FORGED FITTINGS
Products
Get a Free Quote
Toll Free Call :
+91 93216 51417
COPPER NICKEL END CAP forged fittings
The Copper-Nickel End Cap from Nexus Alloys and Steels is a type of forged fitting used to seal the end of a pipe or tube. It provides a protective barrier, preventing the escape of fluid or gas from the pipe. These End Caps are crafted from copper-nickel alloys, which exhibit excellent resistance to seawater, corrosion, and biofouling. Copper-nickel End Caps are typically made from Cu-Ni 90/10 (90% copper and 10% nickel) or Cu-Ni 70/30 (70% copper and 30% nickel). They come in various designs, including seamless and seam-welded variants. The dimensions and sizes of these End Caps adhere to European standards such as EEMUA and DIN. The primary function of a copper-nickel End Cap is to close off the end of a pipe or tube, ensuring a leak-proof connection. These fittings are commonly used in marine applications, offshore platforms, and other environments where corrosion resistance is critical
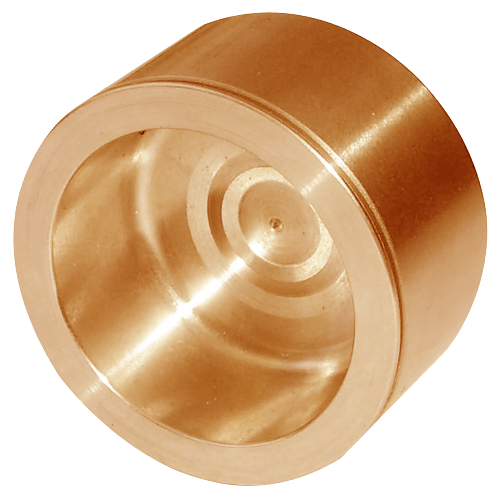
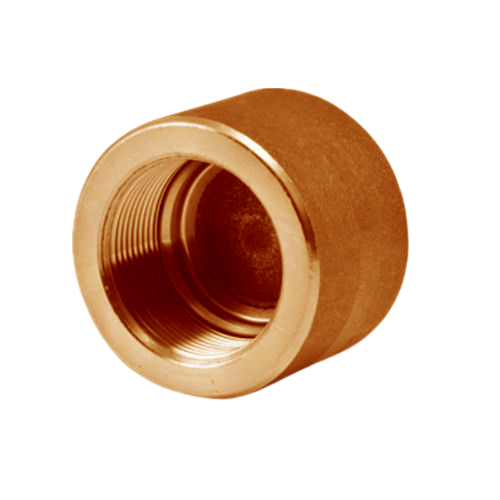
DESCRIPTION
Copper-nickel End Caps by Nexus Alloys and Steels find extensive use in shipbuilding due to their resistance to saltwater corrosion. They are employed in pipelines, offshore rigs, and refineries. These fittings are crucial for desalination systems. Copper-nickel End Caps by Nexus Alloys and Steels play a vital role in maintaining the integrity of piping systems, especially in harsh and corrosive conditions. Their durability, resistance, and reliability make them indispensable components for various industries
Key Features of Copper-Nickel End Cap
- Robust Construction : They are engineered using state-of-the-art forging techniques, resulting in fittings with exceptional strength and durability
- Corrosion Resistance : Crafted from corrosion-resistant alloys, these fittings ensure longevity and reliability even in corrosive environments
- Precision Engineering : Each fitting is meticulously manufactured to exacting standards, guaranteeing dimensional accuracy and consistent performance
- Easy Installation : The design of these fittings facilitates convenient installation, reducing downtime and labor costs
- Superior Resistance to Impingement Corrosion : It is stronger and has superior resistance to impingement corrosion
- Optimized Corrosion Resistance : They have small but important addition of iron and manganese to optimize their corrosion resistance
GRADES
- Copper Nickel C71500 (70/30) : This alloy primarily consists of 70% copper and 30% nickel, with a small amount of iron. It has excellent tensile and yield strength, with tensile strength ranging between 515 and 690 MPa, and yield strength between 195 and 415 MPa. It exhibits excellent resistance to stress corrosion cracking and pitting corrosion. This alloy is widely used in applications that demand high strength and corrosion resistance
- Copper Nickel C70600 (90/10) : This alloy contains 90% copper and 10% nickel, with small amounts of iron and manganese. It has excellent mechanical properties, providing high strength and toughness even at elevated temperatures. The alloy has excellent corrosion resistance, thermal stability, and strength
TECHNICAL SPECIFICATION
- ASTM B467 / ASME SB467 : Standard specification for copper-nickel piping fittings
- ASME B16.11 : Standard for socket welding and threaded forged fittings
- MSS SP-83, 95, 97 : Standards related to butt-welding and threaded fittings
- Socket Weld Cap : Used for socket weld connections
- Threaded / Screwed Cap : Used for threaded connections
- Size Range : Available in sizes from 1/8" NB to 4" NB (both socket weld and threaded)
- Pressure Ratings : Common pressure ratings include 2000 LBS, 3000 LBS, 6000 LBS, and 9000 LBS
SERVICES & CERTIFICATES
- Testing Facility Available Our extensive array of quality assurance measures encompasses Radiography tests, Chemical Analysis, Mechanical Tests, Ultrasonic tests, PMI tests, Hydrostatic tests, Corrosion tests, Metallography Tests, and Miscellaneous tests
- Test Certificates : Our commitment to quality is affirmed through Test Certificates adhering to EN 10204 type 3.1 and 3.2 standards. Furthermore, our certificates incorporate NABL laboratory test reports, assuring the highest standards of quality in our products