END-CAP
Home / Buttweld Fittings / END-CAP
BUTTWELD FITTINGS
Get a Free Quote
Toll Free Call :
+91 93216 51417
COPPER NICKEL END-CAP
The Copper Nickel End-Cap offered by Nexus Alloys and Steels is a high-quality pipe fitting designed for use in various industrial applications. This end-cap is made from a copper-nickel alloy, known for its excellent resistance to corrosion. This makes it particularly suitable for use in harsh environments such as marine and offshore industries. The copper-nickel alloy also provides a unique combination of high strength, excellent formability, and good thermal and electrical conductivity. The “End-Cap” in its name refers to its function in a piping system. It is used to seal the end of a pipe, effectively capping it off. This is crucial in preventing leaks and maintaining the integrity of the piping system
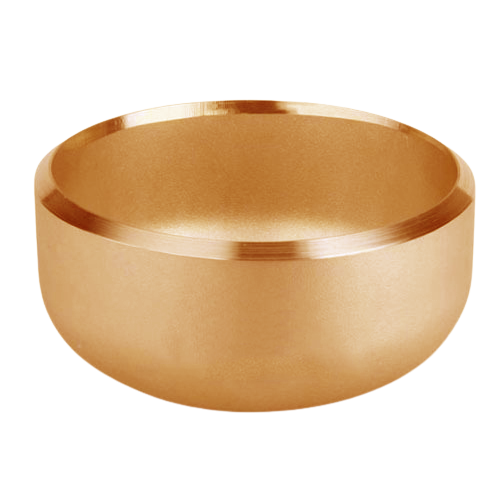
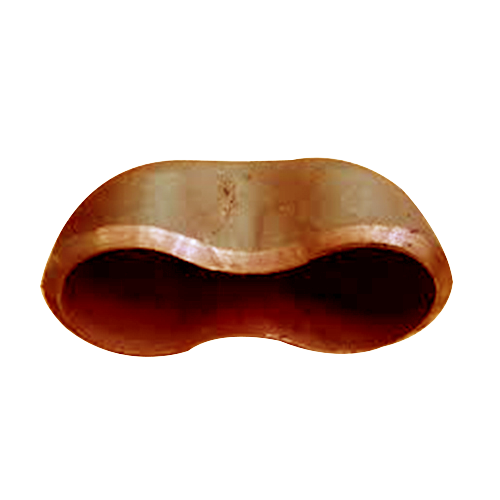
DESCRIPTION
Nexus Alloys and Steels, the manufacturer of this end-cap, is renowned for its commitment to quality and precision. Each Copper Nickel End-Cap they produce undergoes rigorous quality checks to ensure it meets the highest industry standards. In summary, the Copper Nickel End-Cap by Nexus Alloys and Steels is a robust, reliable, and essential fitting that plays a critical role in the assembly and operation of piping systems in various industries. Its unique material properties and the reputation of its manufacturer make it a preferred choice for challenging applications
Key features Copper Nickel End-Caps have
- Material Composition : They are primarily composed of copper and nickel, with small amounts of other elements added to enhance properties such as strength, corrosion resistance, hardenability, weldability, and castability
- Dimensions & Sizes : Copper Nickel End-Caps come in various dimensions and sizes according to Europe standards like EEMUA, DIN & Similar
- Wall Thickness (WT) & Theoretical Weight : The table for Copper Nickel End-Caps lists Wall Thickness (WT) and Theoretical Weight for the pipes which can withstand pressure of 10 bar, 14 bar, 16 bar, 20 bar respectively
- Seamless and Seam Welded Variants : Copper Nickel End-Caps are available in both seamless and seam welded variants
- High Tensile Strength : Copper Nickel End-Caps have high tensile strength, which makes them robust and durable
- Customizability : The design of end caps, diameter, thickness can be customized according to the requirements
- Mechanical Properties : Copper Nickel End-Caps have a density of 0.323 lb/in3 at 68 F and a yield strength (0.2%Offset) of 20000 psi2
- Finishing : They have a smooth polished finish2
GRADES
- Cu-Ni 90/10 (UNS C70600) : Known as Copper Nickel 90/10, this alloy is composed of 90% copper and 10% nickel, blended with iron and manganese to deliver impressive strength and corrosion resistance. Widely applied in marine settings, it exhibits remarkable resistance to seawater, brine water, organic compounds, salts, diluted non-oxidizing acids, and more
- Cu-Ni 70/30 (UNS C71500) : Also recognized as Copper Nickel 70/30, this grade features 70% copper and 30% nickel, with minor additions of iron and manganese enhancing overall strength and corrosion resistance. It surpasses Copper Nickel 90/10 in its resistance to corrosion and erosion, making it well-suited for demanding conditions in marine and industrial services
TECHNICAL SPECIFICATION
- Material : Copper-Nickel alloy (typically CuNi 90/10 or CuNi 70/30)
- Dimension :
- Diameter : Specified in inches or millimeters, based on the pipe size it is designed to fit
- Wall Thickness : Specified in inches or millimeters, often related to the pressure rating
- Pressure Rating : Specified in pounds per square inch (psi) or bar, indicating the maximum pressure the end-cap can withstand
- Temperature Rating : The maximum and minimum temperatures at which the end-cap can operate effectively
- Standards : Compliance with international standards such as ASME, ASTM, etc
- Surface Finish : Can be as-fabricated, polished, or coated depending on the application
- Connection Type : Typically butt-welded or threaded
SERVICES & CERTIFICATES
- Testing Facility Available Chemical Analysis, Mechanical Tests, Ultrasonic test, PMI test , Hydrostatic test, Radiography test, Corrosion test, Metallography Test, & Miscellaneous test
- Test Certificates : Manufacturer Test Certificates as per EN 10204 type 3.1 & 3.2 as well as NABL lab test reports