Get a Free Quote
COPPER NICKEL O’lets
Nexus Alloys and Steels has gained recognition as a leading manufacturer and exporter of Copper Nickel 90/10 and 70/30 products, known for their non-reactive characteristics. These alloys, categorized as high-chromium ferritic heat-resistant alloys, exhibit remarkable resistance to sulfidation, oxidation, and various forms of hot corrosion
Designed for applications within the temperature range of 1,500 to 2,100 degrees Fahrenheit, Copper Nickel 90/10 and 70/30 welding outlets are particularly resilient in challenging environments. However, it's worth noting that their ability to withstand high temperatures is limited in comparison to some other alloys
The elevated chromium content in these alloys contributes to their enhanced resistance against oxidation, corrosion in sulfating conditions, corrosion scaling, and abrasion. Despite these advantages, their high chromium concentration makes Copper Nickel 90/10 and 70/30 socket weld outlets more challenging to manipulate through processes such as bending, spinning, welding, and pulling, as compared to other stainless steel products
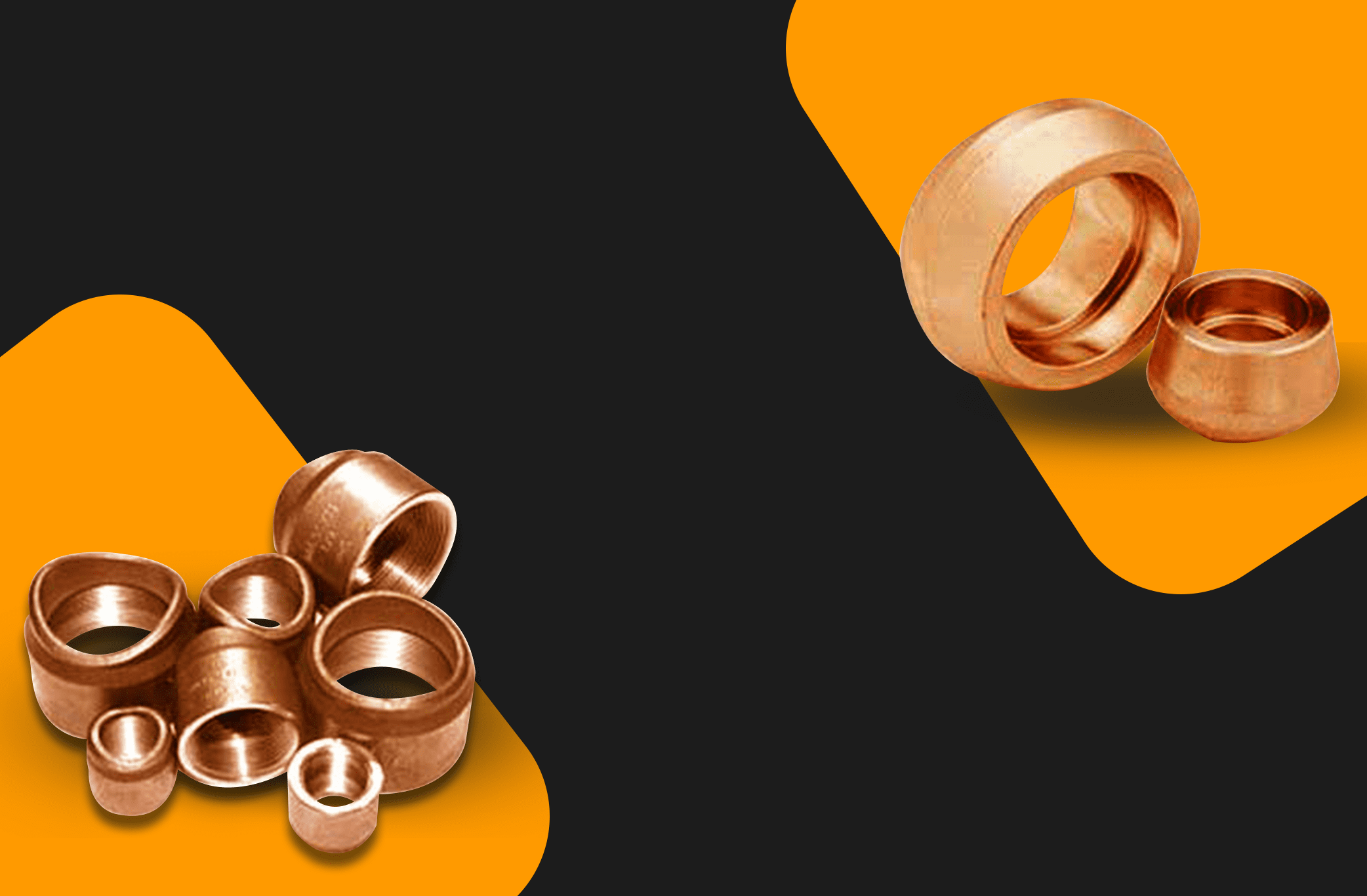
COPPER NICKEL O'LETS
Description
Nexus Alloys and Steels has established itself as a prominent figure in the manufacturing and export of Copper Nickel 90/10 and 70/30 products, showcasing a specialization in alloys celebrated for their non-reactive properties. The focus lies on these alloys being high-chromium ferritic heat-resistant materials, rendering them particularly adept at countering sulfidation, oxidation, and diverse forms of hot corrosion
Tailored for applications spanning temperatures between 1,500 and 2,100 degrees Fahrenheit, the welding outlets of Copper Nickel 90/10 and 70/30 exhibit exceptional resilience in environments notorious for their challenges. It's crucial to acknowledge that, despite their impressive performance, these alloys have limitations in handling extremely high temperatures when compared to certain alternative alloys
The distinctive feature of these alloys lies in their elevated chromium concentration, a characteristic that endows them with superior resistance to oxidation, corrosion under sulfating conditions, corrosion scaling, and abrasion. This heightened resistance, however, comes with a trade-off – the high chromium content makes manipulation through processes like bending, spinning, welding, and pulling more intricate when compared to other stainless-steel counterparts
In essence, the flexible outlets crafted from Copper Nickel 90/10 and 70/30 offer a multitude of advantages. Their robustness and resistance to oxidation and corrosion position them as invaluable assets in demanding industrial applications, reflecting the meticulous engineering and quality manufacturing associated with Nexus Alloys and Steels
APPLICATION
Copper Nickel 90/10 and 70/30 alloys, manufactured and exported by Nexus Alloys and Steels, find widespread applications across diverse industries due to their unique properties. These alloys, renowned for their non-reactivity and heat-resistant characteristics, are instrumental in addressing specific challenges in the following sectors
- Marine Industry : Copper Nickel alloys are extensively used in marine environments, where resistance to corrosion and biofouling is crucial. Their ability to withstand the harsh conditions of seawater makes them ideal for applications such as shipbuilding, offshore structures, and desalination plants
- Oil and Gas Sector : In the oil and gas industry, where corrosion is a persistent concern, Copper Nickel alloys offer a reliable solution. These alloys are utilized in pipelines, heat exchangers, and various components that come into contact with corrosive fluids
- Power Generation : Power plants, especially those dealing with seawater cooling, benefit from the corrosion-resistant nature of Copper Nickel alloys. Their high-chromium content ensures durability in heat exchangers, condensers, and other components critical for efficient power generation
- Chemical Processing : Copper Nickel alloys play a vital role in chemical processing plants, where resistance to oxidation and corrosion is paramount. Their suitability for high-temperature applications makes them valuable in reactors, heat exchangers, and other chemical processing equipment
- Aerospace Industry : In the aerospace sector, where materials must withstand extreme conditions, Copper Nickel alloys find applications in components exposed to high temperatures and corrosive environments. This includes aircraft engines and propulsion systems
- Renewable Energy : The renewable energy sector benefits from the corrosion-resistant properties of Copper Nickel alloys in applications such as solar and wind power. These alloys contribute to the longevity and efficiency of equipment in renewable energy systems
GRADE
- Cu-Ni 90/10 (UNS C70600)
- Cu-Ni 70/30 (UNS C71500)
Types
TECHNICAL SPECIFICATION
Technical Specification (UNS C70600)
Chemical Composition :
- Copper (Cu) : 70%
- Nickel (Ni) : 30%
- Manganese (Mn) : 1.0% max
- Iron (Fe) : 0.03% max
- Lead (Pb) : 0.05% max
Mechanical Properties :
- Tensile Strength : 52,000 psi (359 MPa)
- Yield Strength (0.2% offset) : 20,000 psi (138 MPa)
- Elongation (Mn) : 30%
Corrosion Resistance :
- Excellent resistance in seawater and various chemical environments
- Maintains corrosion resistance at elevated temperatures
Cu-Ni 70/30 (UNS C71500)
Chemical Composition :
- Copper (Cu) : 70%
- Nickel (Ni) : 30%
- Manganese (Mn) : 1.0% max
- Iron (Fe) : 0.04% max
- Lead (Pb) : 0.05% max
Mechanical Properties :
- Tensile Strength : 50,000 psi (345 MPa) min
- Yield Strength (0.2% offset) : (0.2% offset): 20,000 psi (138 MPa) min
- Elongation (Mn) : 30% min
- Hardness (Rockwell B) : 90 max
Corrosion Resistance :
- Excellent resistance to corrosion in seawater and various chemical environments
Application
- Heat exchangers and condensers in power plants
- Marine engineering, including shipbuilding and offshore structures
- Chemical processing equipment
SERVICES & CERTIFICATES
- Testing Facility Available Chemical Analysis, Mechanical Tests, Ultrasonic test, PMI test , Hydrostatic test, Radiography test, Corrosion test, Metallography Test, & Miscellaneous test
- Test Certificates : Manufacturer Test Certificates as per EN 10204 type 3.1 & 3.2 as well as NABL lab test reports